Professional packaging machine repair service for ensuring operational success.
Professional packaging machine repair service for ensuring operational success.
Blog Article
Why Timely Product Packaging Device Repair Service Provider Are Vital for Functional Performance
In the affordable landscape of manufacturing, the duty of prompt product packaging maker fixing services can not be overemphasized. The implications of ignoring these services expand past instant repairs, increasing inquiries regarding tools dependability and total productivity.
Influence of Downtime on Production
Downtime in production can be likened to a ship adrift mixed-up; without a trusted training course, production procedures can promptly divert off track. The influence of downtime, specifically in packaging procedures, can be both prompt and far-reaching. When equipment breakdowns, production halts, causing a stockpile of orders that can strain client partnerships and credibility. Each minute shed translates into revenue loss, as companies have a hard time to fulfill market need and accomplish commitments.
In addition, unintended downtime interferes with workflow, resulting in inadequacies that resound throughout the supply chain. Staff members may be left still, resulting in decreased spirits and performance. In addition, the price of emergency repairs often surpasses that of scheduled maintenance, further stressing monetary resources.
In a competitive landscape, where time-to-market is essential, the capability to preserve constant manufacturing degrees comes to be critical. Downtime not only affects prompt result however can also create a causal sequence that influences stock levels, money flow, and overall functional effectiveness - packaging machine repair service. Thus, understanding and minimizing the influence of downtime is important for manufacturers intending to maintain their competitive side and make certain long-lasting growth
Advantages of Regular Upkeep
Normal upkeep of product packaging devices offers as a critical pillar in making sure continuous production and functional efficiency. By executing a regular maintenance routine, services can dramatically improve the reliability and durability of their devices. Regular assessments permit the timely identification of damage, stopping minor problems from escalating into major breakdowns.
Furthermore, routine maintenance maximizes device performance, making sure that packaging processes run at peak efficiency. This optimization not just enhances throughput but likewise decreases the probability of product issues, thus keeping top notch standards. Furthermore, properly maintained devices add to power performance, minimizing operational expenses connected with extreme power intake.
Along with performance benefits, normal upkeep cultivates a much safer working atmosphere. By ensuring that makers run appropriately, the threat of crashes and injuries created by devices failure is notably lowered. This dedication to security not only shields staff members but additionally straightens with governing conformity, alleviating potential lawful obligations.
Inevitably, purchasing normal upkeep boosts total efficiency, reduces unexpected downtime, and advertises a culture of proactive asset monitoring. This calculated approach makes sure address that packaging operations remain competitive in a busy market, which is important for continual success.
Expense Ramifications of Postponed Repair Services
Neglecting timely repairs on product packaging machines can result in significant financial repercussions for organizations. When machinery breakdowns, production lines can stop, causing lost outcome and delayed shipment routines. packaging machine repair service. Each hour of downtime translates right into not only shed sales however likewise potential charges from customers because of unmet due dates
Additionally, delayed repair services can aggravate existing concerns, resulting in much more extreme damages and raised repair work prices with time. A minor malfunction could intensify into a significant malfunction, demanding pricey components replacement or a total overhaul of the equipment. This can strain budget plans and divert funds from various other critical locations, hindering overall operational growth.
Additionally, companies may deal with enhanced labor costs as employees remain idle or are reassigned throughout extended repair service periods. The longer equipment runs out solution, the a lot more substantial the effect on labor force productivity.
Enhancing Tools Durability
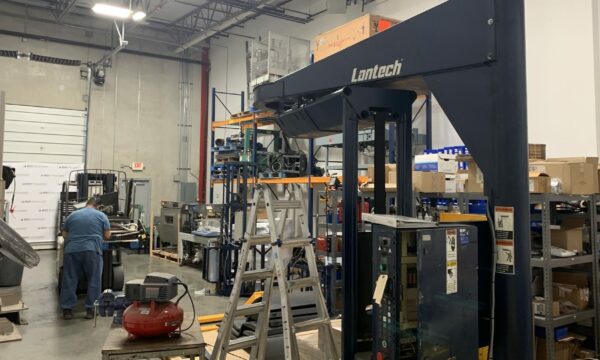
Implementing a regular maintenance schedule can identify deterioration early, stopping tiny issues from rising right into costly failures. This aggressive strategy not only boosts the maker's operational integrity however also maximizes the general production workflow. Operators should also make sure that devices are used according to supplier specs to avoid unnecessary stress and anxiety on essential parts.
Furthermore, spending in high quality substitute parts during repairs contributes to tools durability (packaging machine repair service). Making use of low-grade parts may bring about constant malfunctions, negating any cost savings understood from cheaper repair work. Correct training for drivers on best methods for equipment handling and procedure can also substantially affect the devices's lifespan
Selecting the Right Repair Solution
Selecting the proper fixing solution for packaging makers is necessary for guaranteeing Discover More very little downtime and ideal efficiency. When evaluating potential provider, consider their industry experience and field of expertise in packaging equipment. A business with a tried and tested record in dealing with comparable equipment will likely possess the required experience to diagnose and resolve issues efficiently.
Additionally, assess the accessibility of specialists and their feedback time to solution phone calls. A repair service that provides 24/7 assistance can considerably minimize the effect of unanticipated machine failings. Inquire concerning their maintenance programs, as positive service can prevent expensive break downs and expand the lifespan of your devices.
Review client reviews and reviews to evaluate the integrity and high quality of the service. A trustworthy repair work service must have a background of satisfied customers that can confirm to their expertise and performance. Finally, consider the prices involved, consisting of parts and labor. While affordability is essential, prioritize value-- ensuring that the service meets your functional requirements without jeopardizing high quality. By meticulously picking the right fixing service, services can improve their operational effectiveness and lessen disruptions in manufacturing.
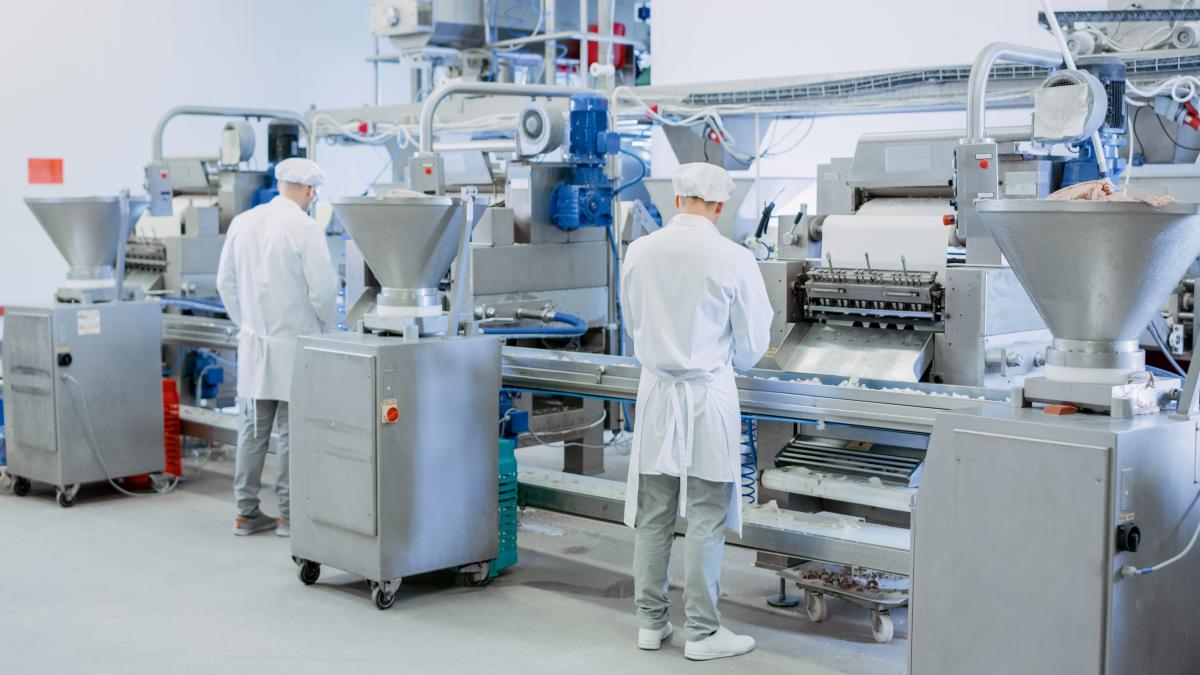
Conclusion
In verdict, prompt packaging device repair work solutions play a crucial function in preserving functional effectiveness. Routine upkeep and timely repair work offer to reduce minor concerns before they intensify, thus ensuring optimum device performance.
Report this page